Quick Info:
MIDI-plant
Scrap Tire Recycling
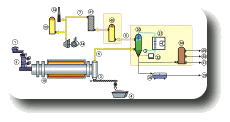
|
 |
 |
 |
 |
|
 |
Dirk Gerlach Engineer
|
|
|
|
Processes description calcination
To calcine mineral ores means to change the chemical composition by a thermal process or to drive off a volatile fraction.
Compared to pyrolysis the absence of oxygen is not necessary in this process. Directly heated as well as indirectly heated rotary kilns can be used for calcinating.
Applications
Conversion of Carbonates to Oxides
The process of calcination derives its name from its most noted application, the decomposition of calcium carbonate (limestone) to calcium oxide (lime).
The process of any conversion of carbonates to oxides is callded "calcination" such as the decomposition of zinc carbonate to zinc oxide.
The so-called "shrinking core model" with surface reaction rate controlling mechanism is the best model, which describes the reaction.
For maximizing the speed of calcination in rotary kilns the particle size has to be minimized.
Cement Industry
The most common application of calcination is the cement industry.
After mining, grinding and homogenisation of raw materials the first step in cement
manufacture is calcination of calcium carbonate followed by burning the resulting calcium
oxide together with silica, alumina, and ferrous oxide at high temperatures to form clinker. The
clinker is then ground or milled together with gypsum and other constituents to produce cement.
Generating Aluminium from Bauxite
The raw material bauxite reacts with caustic soda to aluminium hydroxide.
Rotary kilns are used to convert aluminium hydroxide into aluminium oxide by driving off water.
Next to the calcination, the aluminium oxide undergoes an electrolytic process to gain aluminium.
Further Applications
A lot of chemicals are obtained by calcination, such as pigments, welding additives and so on.
|
|
Dipl.-Ing.(FH) Dirk Gerlach Passion for Innovation
|
|  |
 |
 |
 |
|
|
A Service of LEO GmbH.
|