Quick Info:
MIDI-plant
Scrap Tire Recycling
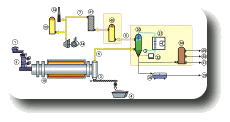
|
 |
 |
 |
 |
|
|
Dirk Gerlach Engineer
|
|
|
|
Technical details about DGE thermolysis plants
Function
The thermal process is completely closed!
By means of an air-tight sluice the scrap tire granulate is carried into the rotary kiln.
The granulate is heated up in a pressure-less reactor and it decomposes into gas and elementary carbon.
The filling materials contained in the tire and the carbon will be discharged and conveyed into a certified carbon dust hopper (silo).
The resulting hot process gases are led through a condensation unit and cooled down. Thereby the main part of the gas becomes liquid.
The condensate - which is similar to diesel - is discharged and is stored in certified tanks until the condensate is collected or used.
Quantity- and energy distribution
For an initial survey of the nominal quantities and energy flows for the plant type MIDI:
Input scrap tire granulate |
Input solids |
Output condensate |
Output (permanent-)gas |
600 kg/h |
240 kg/h |
300 kg/h |
60 kg/h appr. 55 Nm³/h |
5,4 MW |
1,8 MW |
3,2 MW |
0,4 MW |
These values can differ due to different process parameters. (see also CalRecovery-Report No. 1364 California 1995).
Applications
- Production plant for technical oils / solids: depending on process parameters the product quality can be changed significantly
- Decentral energy station: Using the alternative 'gas' we suggest a combination with a steam boiler. The electrical power by a multifuel engine (e.g. from MTU) supplies approx. 500kW surplus.
- Peak load electricity generation plant: Using the alternative 'electric' we suggest a combination with a windmill. With a peak load CHP up to 12 MWh/d can be generated at still air.
Environmental protection action
The following environmental protection actions are included by default:
Oil
- Certified storage tanks
- Flexible connecting pipes according to chemical standard, leakage-free clutches
- Stop-cock before and after serviced modules
- Unit racks with safety sump for hazardous goods
In sensitive areas it may be required to have as an additional security action a sealed surface.
Gas
- Seals and sluices are charged with inert gas
- Gas scrubber for elimination of hydrogen sulfid from the permanent gas ( THIOPAQ® )
- Additional security filter with active coal for guaranteed elimination of PACs (ex.g. DESOTEC)
Dust
- Housing of the granulator with dedusting unit
Fine dust
- Condensation scrubber: the fine dust is discharged securely from the process gas.
Heavy metals
- Condensation scrubber with 2-phase centrifuge. By means of the centrifuge sludges are being separated and disposed.
- Additional security filter with active coal for guaranteed elimination of heavy metal compounds (ex.g. DESOTEC)
Due to the process all substances which are not gaseous at process temperature remain in the solid.
All substances which condensate above the condensation temperature, are absorbed in the condensation scrubber.
Plant security
The plant is equipped with an automatically control system AutomationX which offers an onsite operation as well as a remote support.
AutomationX has experiences in large-scale waste processing and offers substantial log-and mathematical functions which are required for a
verifiable operation and defined qualities. The plant is as well equipped with a substantial sensor technology to transfer
all relevant measurements at any time to the control system. The relevant sensors are designed redundnat according to SIL-concept.
In case of incidence (e.g. unusual measurements, exceeding of given limits) a warning is given to the responsible operator and the plant
goes automatically into a secure operational state (i.e. the input material is discharged from the rotary kiln). DGE offers the service of
a nationwide central control room for times when local staff is unavailable.
History of plant concept '... with condensation'
 |
Salzgitter
The plant in Salzgitter (built in 1983/84) with a throughput of 4-6 t/h was equipped as the first industrial plant with a condensation.
With the destructive printed matter 12/3823 the German government answers in 1992 a query initiated by the party 'Die Linke' (environmental compatibility assessment without public participation, accidents etc.).
Afterwards the plant was modified and a regular environmental compatability assessment without complaints was executed and finally the plant was put into operation in 1996. The plant was successfully in operation for several years.
The plant was operated with especially supervision requiring waste. A long-term feasability could not be reached because the possible products were due to their chemical pollution only hazardous waste.
Dr. Rosemann carried out his dissertation 'Products of waste pyrolysis' in 1998 at the plant and discovered that temperature, filling degree and residence time cause significant differences.
|
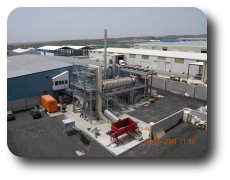 |
Limassol
The plant was built for CBp (later: Carbon Green) by TechTrade (project leader: Dirk Gerlach) and was commissioned in 2009 by DGEngineering.
Originally the plant should be erected in Czongrad (CZ) and displace a batch plant for scrap tyres. Because of serious safety and environmetal protection deficits the authorities refused permission for reconstruction.
As new location for the almost ready plant Cyprus was defined because with the planned stage 1(which was only an intermediate step) the complete scrap tyres from Cyprus could be processed.
The main focus of the operator was on the CarbonGreen (Carbon black) and the condensation stage served only the energy removal from the process in terms of condensate oil.
The engaged venturi-washer functioned technically well, but could only be adjusted mechanically due to economical reasons. Therefore the washer could not be automatically adapted to different process conditions.
|
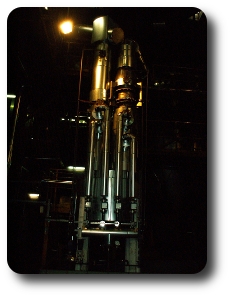 |
Herne
The soil cleaning plant Herne from company Sitatreats massive and complex contaminated mineral wastes which are nonbiodegradeable, including dioxine- and furan-contaminated soils.
To reduce the internal dust loading (i.e. reduction oof maintenance effort) an additional scrubber unit was installed in 2012. This unit functioned technically excellent, but it took too much energy from the process.
Due to the (ever changing) heavy metal pollution of the condensate there was no economical solution and, simultaneously, energy costs rose because there was additional need for fuel. Because of these economical reasons this unit was decommissioned and later dismantled
|
|
|
Dipl.-Ing.(FH) Dirk Gerlach Passion for Innovation
|
|  |
 |
 |
 |
|
|
A Service of LEO GmbH.
|