Quick Info:
MIDI-plant
Scrap Tire Recycling
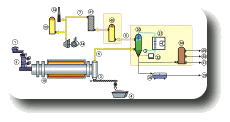
|
 |
 |
 |
 |
|
|
Dirk Gerlach Engineer
|
|
|
|
Massbalance sample of a MIDI-Quad project
Emissions
To get a first impression of emisssions the following categories are interesting:
Fine dust
Smell
Matured scrap tires which can not be exported due to age reasons contain significantly less smelling softeners than new tires.
The scrap tire granulate is almost odorless.
The combustion air is being deducted from the open storage dump to install (another) safety to reduce odor.
Gases
The gas which is led through ex.g. THIOPAQ® and the active coal filters contains mainly methane, carbondioxide, hydrogen, carbon monoxide. There are also small amounts of ethane, propane and butane (propane and butane are the two components of autogas).
The gas will be converted into electricity by means of a gas engine. The off-gas then contains carbon dioxide and water.
So, in a norminal case (i.e. 600 kg/h input) there will be emissions of approx. 600 - 800 Nm³/h Abgase.
Noise
The processing of scrap tires to rubber granulate is done in a housed granulator.
Condensate oil
The condensate oil is kept in a completely closed system and does not exit the system!
In case of a pipe line break there are sumps for hazardous goods integrated in the plant. If the sensor technology detects a break the broken pipe line is automatically shut down. Afterwards the plant goes into a secure operational state (i.e. the input material is discharged from the rotary kiln).
The oil is being stored in a certified tank and is collected four times a week (each approx. 30m3).
Solid 'coke'
The product received contains up to 83% elementary carbon and the filling material of the tires, mostly silicium.
According to process parameters there may be up to 2% of sulphur in the coke.
The removal/collection of the certified carbon dust silo with filter is done 8 times a week.
The carbon green corresponds to a large extent to the specification of active coal N660.
Sulphur
According to process parameters the sulphur remains as elementary sulphur in the solid or it goes as sulphur compound into the condensate or ideally as hydrogen sulphide into the gas phase.
With the THIOPAQ®process the hydrogen sulphide is separated from the permanent gas and will be separated as elementary by means of a biological treatment.
During nominal operation there will be maximal 280 kg/d of elementary sulphur generated.
According to safety data sheet sulphur does not fulfill the PTB-criterias (persistent/bioaccumulative/toxic).
Theoretically maximal incidence emissions
In a worst-case scenario (i.e. sudden blackout of gas treatment/condensation) the temperature in the reactor is lowered beneath 300°C within 15 minutes. Theorectically the plant could achieve 25% of the hourly output.
Steady variations are detected by the system itself (e.g. presssure measurements) and the plant goes automatically into a secure operational state.
Substance |
critical temperature transfer into gas phase |
bagatelle mass flow according to TA-Luft |
tire analysis |
incident mass flow |
|
Arsenic |
613 °C |
0,0025 kg/h |
10 mg/kg presumed |
0,003 |
|
Benzo(a)pyren |
°C |
0,0025 kg/h |
|
|
|
Benzene |
°C |
0,05 kg/h |
|
|
|
Cadmium |
767 °C |
0,0025 kg/h |
10 mg/kg |
0,003 kg/h |
|
Mercury |
356 °C |
0,0025 kg/h |
0,17 ppm |
0,00005 kg/h |
|
Sulphur oxide |
- |
20 kg/h |
1% |
4 kg/h |
|
Dust |
- |
1 kg/h |
|
|
|
For this kind of incidence an emergency flare is installed to burn all carbon hydrides safely.
The possible short-term heavy metal pollution on the contrary is within bagatelle mass flow limits for continuous operation. For the approval process one has to take a closer look at this.
|
|
Dipl.-Ing.(FH) Dirk Gerlach Passion for Innovation
|
|  |
 |
 |
 |
|
|
A Service of LEO GmbH.
|